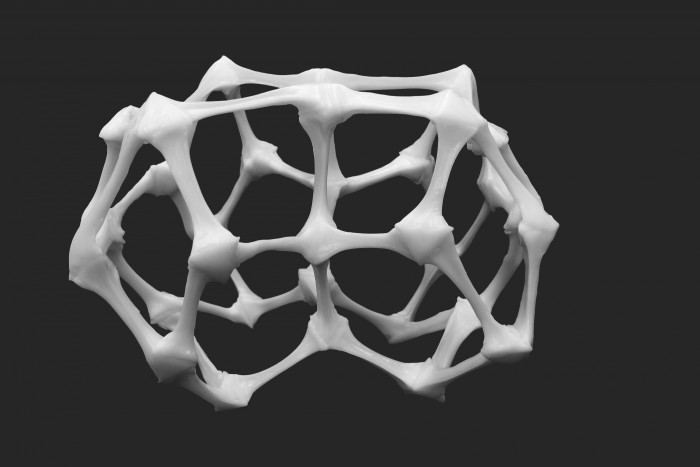
A group of students from the Architectural Association DRL have proposed a flexible, automatic robotic fabrication system for temporary architecture. The construction of infrastructure contributes to 70 per cent of the overall waste production in London. The project, Osteobotics, proposes that a biodegradable, reusable material be used to create temporary structures.
Using Polycaprolactone, a biodegradable polyester, the students created a framework for temporary pavilions or installations. The material is able to stretch when heated and hold its compressive strength when cooled. “The dynamism and reusability of the system results in a variety of temporary architectural applications, where the manufactured lattice is manually assembled on-site using heat,” wrote the students.
The project was constructed using robotic arms and is part of a recent study into the architectural potential of robotics. Once the Polycaprolactone melts at 60 degrees centigrade, one robotic arm stretches the soft, pliable material while another robotic arm cools the material with freezing spray. The process results in a plastic structure that looks almost bone-like.
The aim of the project was to shift the existing perception that parts can only be made in a factory and infrastructure requires vast amounts of labour and rigging to construct. “The fabrication system is enclosed in a mobile unit, shifting the existing paradigm of the factory away from rigid, prefabricated components and towards custom architecture utilising phase-changing materials with on-site robotic fabrication. This allows for minimum manual assembly, greatly decreasing the construction and assembly times and removing the necessity for scaffolding,” wrote the students.